Ever wondered how those perfectly shaped rings, tubes, or coils in machinery and jewelry come to life? Well, we’ve got the answer, and it’s simpler than you might think. It all boils down to a tool that might not get much limelight but plays a crucial role in manufacturing and craftsmanship: the mandrel.
At its core, a mandrel is a game-changer in the world of precision and design. It’s the unsung hero behind the scenes, ensuring everything from metal pipes to delicate wire jewelry maintains the perfect shape during production. Let’s dive into the fascinating world of mandrels, exploring how this tool shapes not just materials, but the very industries it supports. Join us as we unravel the mystery behind this essential tool, showcasing its significance and versatility across various applications.
Understanding the Basics: What Is a Mandrel?
Building on the significance of mandrels in enhancing precision in manufacturing and craftsmanship, let’s dive into what a mandrel actually is. A mandrel is a tool used to support, shape, and secure materials being worked on. Typically cylindrical in shape, these tools are essential in processes where materials need to maintain a specific shape or dimension during manufacture or modification.
Mandrels come in various forms, each designed for specific tasks. For example, in metalworking, a solid mandrel might aid in bending tubes to ensure they don’t collapse. In the realm of jewelry making, a tapered mandrel helps jewelers form rings to exact sizes. This versatility underscores the mandrel’s role across different industries, from intricate artistry to heavy-duty manufacturing.
The core function of a mandrel, however, remains constant: to provide an internal support structure that materials can be shaped around. Whether it’s preventing deformation during the bending of a pipe or ensuring the uniform winding of wire for crafting purposes, mandrels offer the necessary stability for achieving precision.
Materials like wood, metal, and even plastic can be crafted into mandrels, thus providing a wide range of hardness and flexibility for various applications. Furthermore, mandrels can be specialized; some are designed to expand within a workpiece, offering internal support for delicate operations, while others are used in the process of machining to hold workpieces in lathes securely.
A mandrel serves as an indispensable tool in the toolkit of craftsmen and manufacturers alike. Its ability to ensure the accurate shaping and structuring of materials across a broad spectrum of industries illustrates its critical role in achieving design perfection and functional precision. As we’ve seen, regardless of the project at hand, there’s likely a mandrel that’s perfectly suited to the task, showcasing once more the sophistication and versatility of this essential tool.
The Significance of Mandrels in Manufacturing
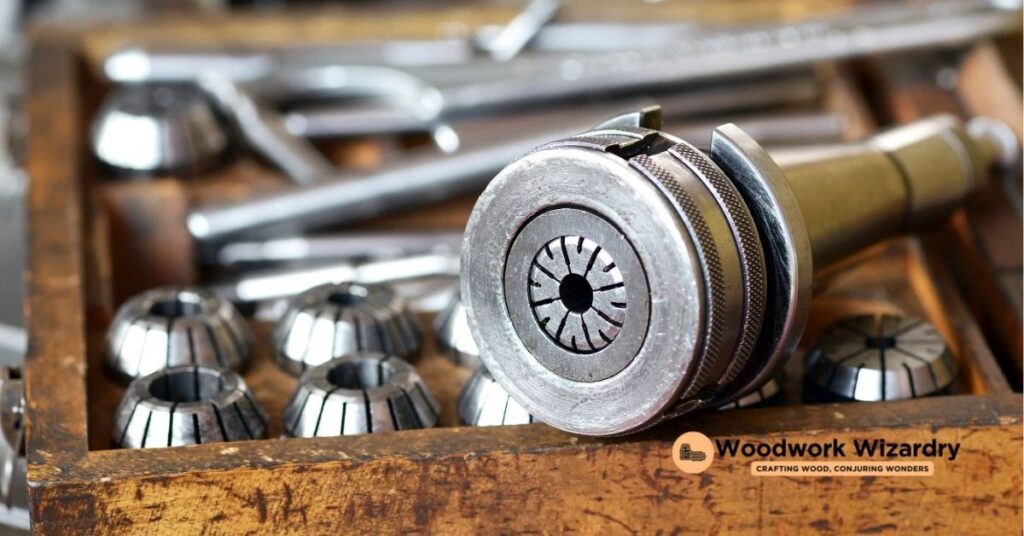
Delving deeper into the intricacies of manufacturing, we find that mandrels play a pivotal role in the production process, bringing an unmatched level of precision and efficiency to the table. These tools are not just about shaping; they’re about ensuring that each piece, whether it’s a metal pipe or a delicate ring, meets the exact specifications required. This level of accuracy is crucial in industries where even the smallest deviation can lead to significant issues down the line.
Mandrels offer support in ways other tools cannot, acting as the backbone for materials as they undergo transformation. In metalworking, for instance, a mandrel ensures that tubes bend without collapsing, maintaining a smooth and uniform shape throughout. This is especially important in applications such as aerospace and automotive industries, where the integrity of each component can directly impact safety and performance.
In the realm of jewelry making, mandrels contribute to the artistry and precision of the craft. They allow jewelers to shape rings and bracelets with confidence, knowing that every curve and contour will be consistent. This consistency is paramount not just for the beauty of the pieces but also for their fit and comfort.
Moreover, mandrels are adaptable tools. Their versatility extends across various materials and applications, from woodworking to plastic molding. This adaptability makes them indispensable in workshops and factories alike, where they cater to a wide range of projects and production needs.
Their significance also lies in their contribution to operational efficiency. By providing a reliable foundation for shaping materials, mandrels reduce the risk of errors and rework, saving time and materials in the process. This efficiency is vital in keeping production lines moving smoothly and ensuring that deadlines are met without compromising quality.
The significance of mandrels in manufacturing cannot be overstated. They are key players in the production process, responsible for the precision, efficiency, and versatility that modern industries demand. Through their support, materials are shaped and transformed with accuracy, ensuring that each product meets the high standards of today’s market.
Types of Mandrels and Their Specializations
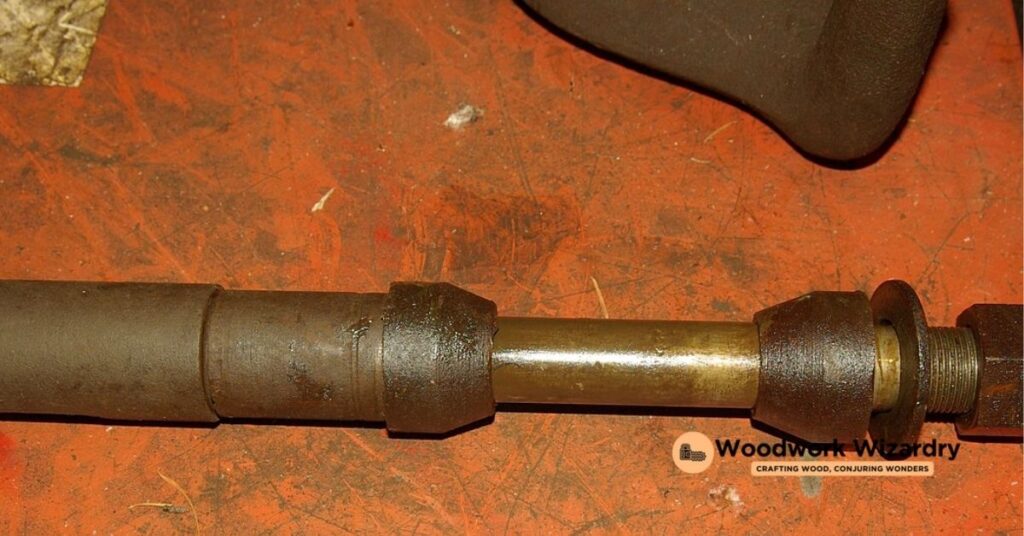
Building on the indispensable role of mandrels in various industries, it’s fascinating to explore the different types that exist and their unique specializations. Mandrels are not one-size-fits-all; rather, they are tailored to specific tasks, each designed to optimize precision and efficiency in different applications. Here, we delve into some of the most common types of mandrels and what sets them apart.
- Solid Mandrels: These are primarily used for holding and supporting work in lathes. Solid mandrels boast simplicity and durability, making them perfect for tasks requiring stability without internal adjustments.
- Expansion Mandrels: Offering versatility, expansion mandrels have adjustable diameters to grip the inside of workpieces securely. They excel in precision tasks, where internal support without marring the material is crucial.
- Screw Mandrels: Specifically designed for holding items that need to be filed, polished, or machined, screw mandrels fit into drill chucks or lathes. They’re indispensable in jewelry making, where fine detailing is paramount.
- Shell Mandrels: Utilized for workpieces with hollow sections, shell mandrels provide external support to prevent collapse or deformation during the machining process. They’re ideal for intricate aerospace and automotive parts.
- Taper Mandrels: These are used for aligning and sizing holes, ensuring a precise fit. Taper mandrels are essential in assembly operations where components must fit together with exact tolerances.
Each type of mandrel has been developed with a specific purpose in mind, reflecting the versatility and breadth of applications they serve. Whether for aerospace engineering, automotive manufacturing, jewelry design, or metalworking, mandrels help achieve the precision and quality demanded by today’s sophisticated production standards. Through these specialized tools, industries can maintain the integrity of components, reduce errors, and uphold high-quality outcomes in every project.
Selecting the Right Mandrel for Your Project
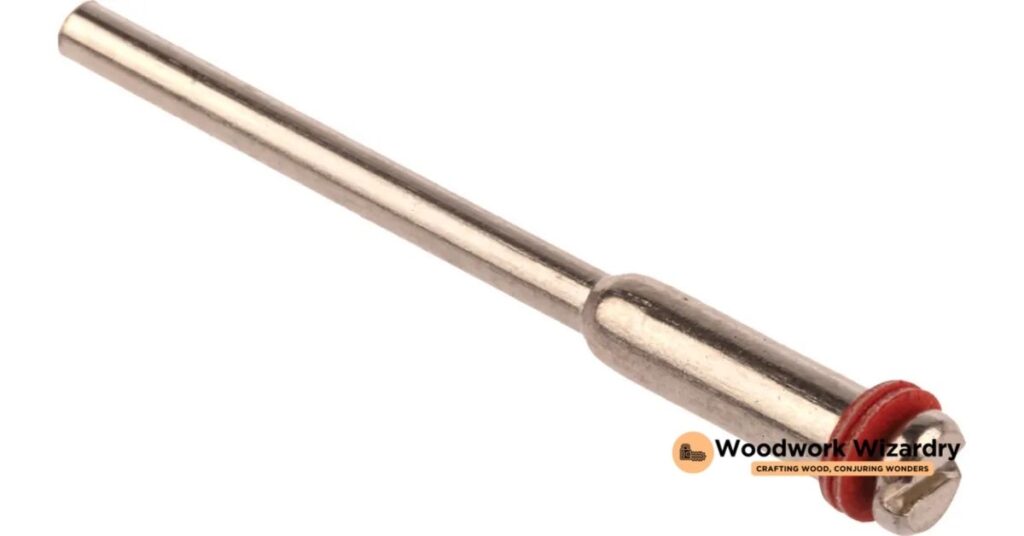
Selecting the appropriate mandrel for your project is significant, as it directly influences the quality, precision, and efficiency of the work. The previous paragraphs provided an overview of the different types of mandrels and their applications in various industries. Here, we’ll guide you on how to pick the ideal mandrel, considering key factors and the nature of the project at hand.
Identify the Material and Shape Requirements
Understanding the material you plan to work with and the desired final shape is the first step. For instance, solid mandrels offer unmatched stability and are perfect for materials that require high force without deformation. If you’re aiming for versatility, especially with varied internal diameters, expansion mandrels might be your go-to option.
Consider the Precision Level Needed
Each project demands a certain level of precision. Screw and taper mandrels are excellent choices for projects that require exact fittings, such as in aerospace or automotive parts. High precision tasks, particularly in jewelry making or intricate metalworking, benefit greatly from these types.
Evaluate the Project’s Scale and Volume
The size and quantity of items you’re working on should influence your choice. For large-scale productions, shell mandrels can be highly efficient, allowing quick changes between tasks. Conversely, for detailed, one-off projects, a screw or expansion mandrel offers the adaptability and fine control needed.
Assess Compatibility with Existing Equipment
Ensure the mandrel you select is compatible with your current machinery or tools. This compatibility maximizes the productivity and safety of your operations. Check the specifications carefully before making a decision.
By considering these aspects—material requirements, precision level, project scale, and equipment compatibility—you’ll effectively choose the right mandrel, ensuring your project’s success and the desired outcome’s quality. Remember, the correctly selected mandrel not only improves work efficiency but also contributes significantly to achieving precise and high-quality results.
Innovative Uses of Mandrels
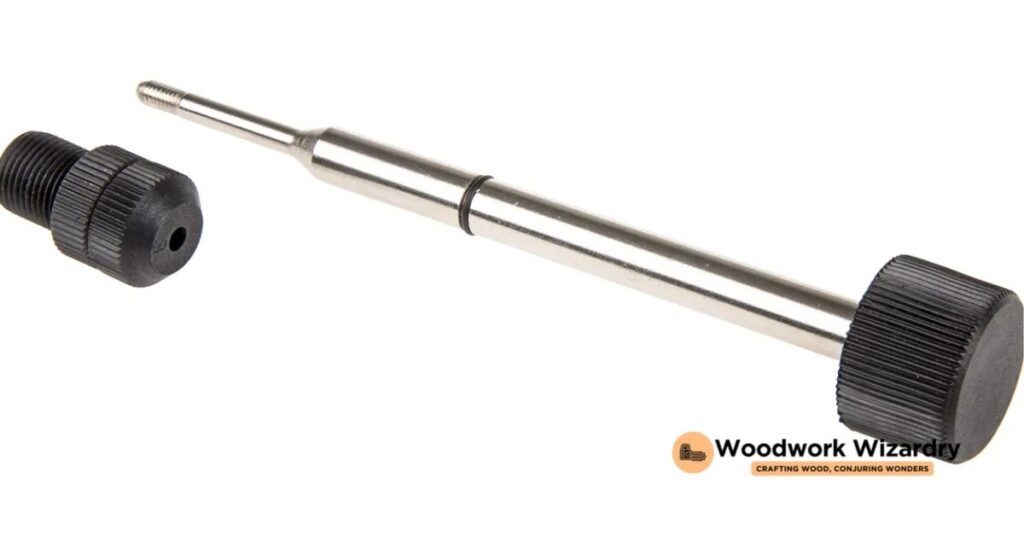
Building on the essential knowledge of mandrels, their types, and the critical factors for selecting the right one, we dive into the innovative ways these tools are being utilized across various industries. Mandrels don’t just play a crucial role in manufacturing and metalworking but also pave the way for creativity and innovation in less traditional areas.
One fascinating application is in the creation of composite materials. Engineers use mandrels to shape and cure composite fibers, such as carbon fiber and fiberglass, into strong, lightweight structures for aerospace and automotive parts. The precision provided by a mandrel ensures that these materials meet the strict tolerances required for high-performance applications.
In the medical sector, mandrels find a niche yet vital role. They’re used to manufacture medical tubing, stents, and catheters. The ability to create tubes with exact interior dimensions and smooth surfaces is paramount in medical applications, affecting both the functionality and the safety of these devices.
Another innovative use comes from the jewelry industry, where mandrels are not only used in shaping and sizing rings but also in creating intricate designs with metals. This practice showcases the versatility of mandrels, proving they’re not limited to heavy industrial use but also excel in fine, detailed craftsmanship.
Lastly, in the field of electronics, mandrels are instrumental in winding coils used in transformers, motors, and inductors. The precision in coil winding is critical for the performance of electronic devices, highlighting the significance of mandrels in achieving the necessary accuracy and consistency.
Exploring the varied applications of mandrels illuminates their ubiquitous yet often overlooked contributions to both everyday products and cutting-edge technology. Through their innovative uses, mandrels continue to shape the future of manufacturing, reaching beyond traditional metalworking to drive advancements in numerous sectors.
Conclusion
We’ve journeyed through the pivotal role of mandrels in various industries, underscoring their indispensable value in precision craftsmanship and manufacturing. From the aerospace sector to the delicate art of jewelry making, mandrels prove their worth by enabling the creation of complex and precise components. Their versatility extends across a spectrum of applications, illustrating their critical function in not just traditional metalworking but also in innovative technological advancements. As we’ve seen, whether it’s in shaping composite materials or winding coils for electronics, mandrels are at the heart of manufacturing excellence. They’re not just tools; they’re the unsung heroes of the manufacturing world, shaping the future one precise component at a time.
Related Posts:
- Top Beginner-Friendly Woods: Find Your Perfect Match for Woodworking
- Top 10 Best Woods for Turning: Softwoods to Exotics
- Ultimate Guide: How to Carve a Wood Spirit – Techniques & Care
- Prevent Splitting: How to Keep Green Wood Intact
- Ultimate Guide: How to Oil a Mini Chainsaw for Peak Performance
- Easy Guide: How to Untangle a Chainsaw Chain Safely & Quickly
- Is Woodworking Hard? Debunking Myths & Mastering the Craft
- What Is a Mandrel? Exploring Its Types and Industrial Applications
- Why Is Teak Wood So Expensive? Unveiling the Reasons