Curious about pallet wood and what it’s actually made of? You’re not alone. As DIY enthusiasts and upcycling advocates, we’ve seen the explosion in popularity of pallet wood projects—from rustic furniture to wall art and garden planters.
Most shipping pallets are crafted from softwoods like pine and spruce due to their affordability, availability, and lightweight properties. But, you’ll also find hardwood pallets made from oak or maple when greater durability is needed. What makes these wooden platforms so appealing for repurposing isn’t just their accessibility, but the unique character each piece carries from its journey through the shipping industry.
What Is Pallet Wood Made Of: An Overview
Pallet wood comes primarily from two categories of trees: softwoods and hardwoods. Softwoods like pine, spruce, and fir constitute approximately 80% of all shipping pallets due to their abundance and cost-effectiveness. These lighter woods are perfect for standard shipping needs where extreme durability isn’t required.
Hardwoods such as oak, maple, and hickory make up the remaining 20% of pallet materials, offering superior strength for heavier loads. These dense woods withstand greater weight and resist damage better than their softwood counterparts, making them ideal for international shipping or transporting heavy machinery.
Most pallets in North America are constructed according to standardized dimensions (48″ x 40″) established by the Grocery Manufacturers Association. European pallets follow different standards, typically measuring 1200mm x 800mm (approximately 47″ x 31″).
The actual construction of a pallet includes three main components:
- Deck boards: The flat horizontal pieces that form the top and bottom surfaces
- Stringers: The long support pieces that run perpendicular to the deck boards
- Blocks: Used in some designs instead of stringers to create four-way entry points
Treatment methods vary based on intended use and destination. Heat-treated pallets, marked with “HT,” have been kiln-dried to eliminate pests and are approved for international shipping. Chemically treated pallets, previously treated with methyl bromide (marked “MB”), are less common today due to environmental concerns.
Manufacturers often incorporate recycled wood into pallet production, with some modern pallets containing up to 40% reclaimed material. This practice reduces environmental impact while maintaining structural integrity through careful quality control processes.
Common Types of Wood Used in Pallets
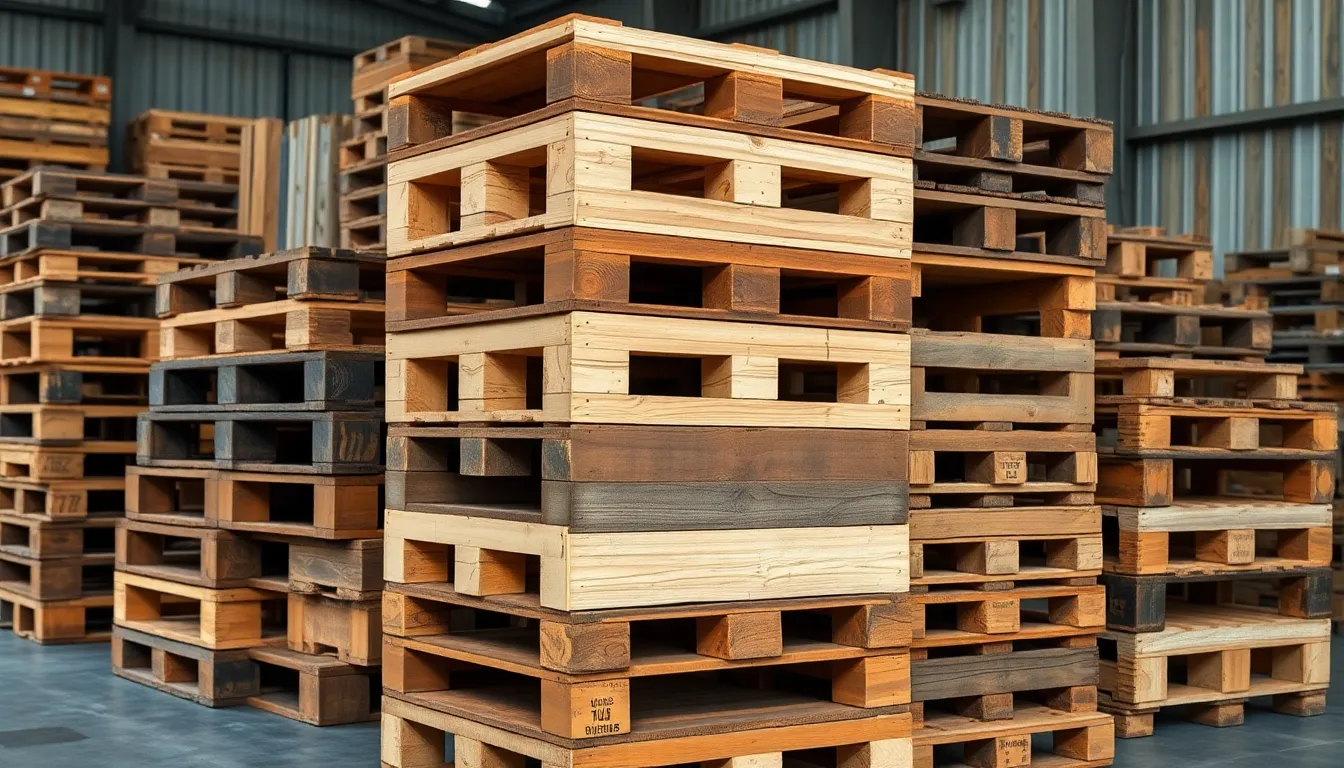
Pallet wood composition varies widely depending on intended use, regional availability, and cost considerations. Various wood species offer different benefits in terms of strength, durability, and price point when used for pallet construction.
Softwoods: Pine, Spruce, and Fir
Softwoods dominate the pallet industry due to their widespread availability and cost-effectiveness. Southern Yellow Pine (SYP) accounts for approximately 18.9% of all pallet wood by volume, making it the most common softwood choice for manufacturers. Many shipping companies prefer spruce for standard pallets because it offers a good balance between strength and weight. Fir represents another popular softwood option that’s frequently combined with pine in pallet production to achieve optimal structural properties. These softwoods typically comprise around 80% of pallet materials in circulation today, serving the needs of industries where moderate load capacities are sufficient.
Hardwoods: Oak, Maple, and Birch
Hardwoods provide superior strength and longevity for pallets designed to handle heavier loads or harsh conditions. Oak stands as the predominant hardwood choice, constituting about 17.1% of pallet wood volume, and it’s prized for its exceptional durability in demanding shipping environments. Maple pallets offer excellent resistance to wear and tear, making them suitable for repeated use in industrial settings. Birch, while less common, brings natural decay resistance properties that extend pallet lifespan, particularly in environments where moisture exposure is a concern. Companies frequently select hardwood pallets for valuable or heavyweight cargo that requires additional protection during transit and storage.
The Manufacturing Process of Wooden Pallets
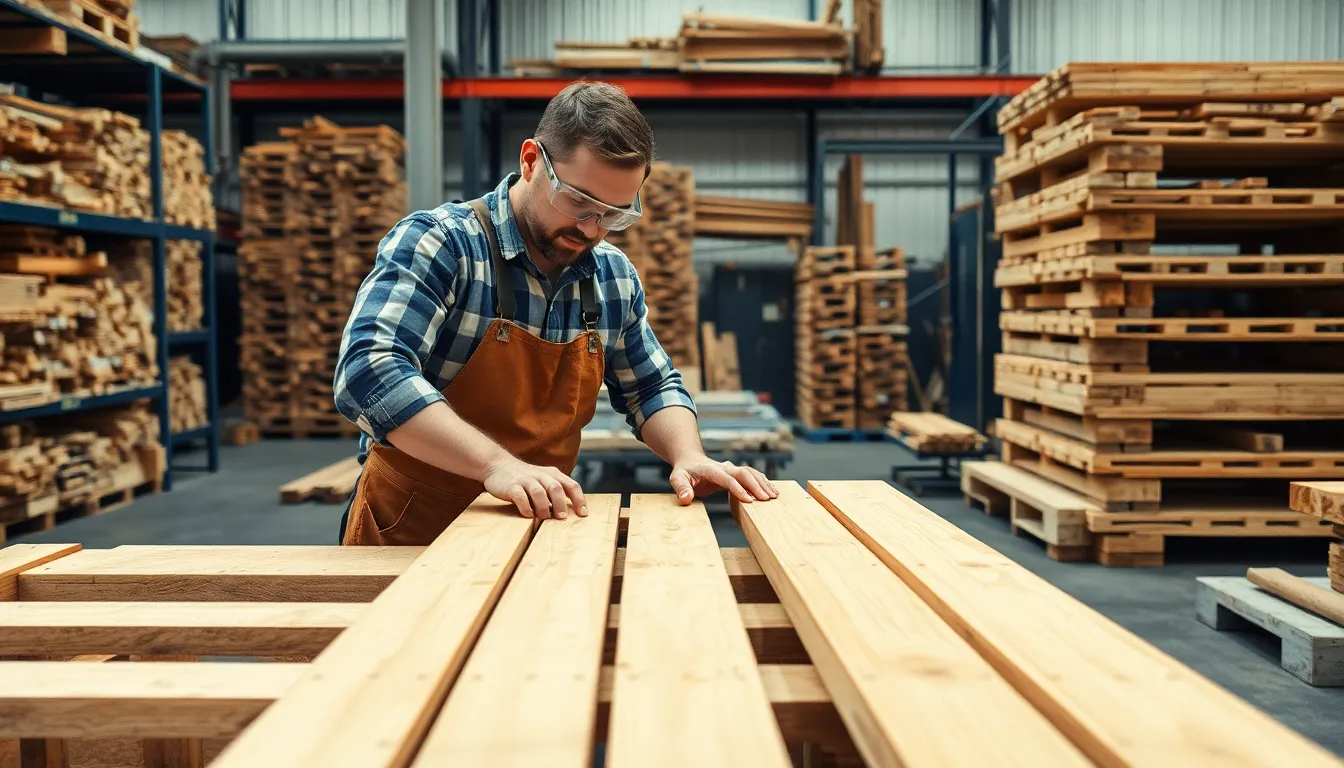
The manufacturing process of wooden pallets follows several exact steps to create durable, functional shipping platforms. Each stage contributes to the final product’s reliability and suitability for industrial use.
Material Selection
Material selection forms the foundation of pallet production, with manufacturers choosing exact wood types based on availability and intended purpose. Softwoods like pine dominate the selection process for lighter pallets due to their abundance and cost-effectiveness. Oak and other hardwoods are preferred for creating stronger pallets that can withstand heavier loads and more rugged conditions. The choice between softwood and hardwood directly impacts the pallet’s strength, longevity, and price point.
Cutting and Assembly
Cutting and assembly transform raw lumber into functional pallets through precise measurements and strategic construction techniques. Wood planks are cut to standardized dimensions according to pallet specifications, then arranged in the classic pallet formation. Metal fasteners, typically nails or screws, secure the components together, creating the structural integrity needed for industrial use. Assembly methods vary from manual construction to automated systems in larger manufacturing facilities, but all focus on creating strong joints between the deck boards and support components.
Finishing
Finishing processes enhance pallets’ durability and compliance with international shipping regulations. Some pallets undergo sanding to remove rough edges and splinters, improving handling safety. Staining might be applied to certain pallets for aesthetic purposes or brand identification in specialized applications. These finishing touches don’t just improve appearance—they extend the pallet’s usable lifespan and reduce potential damage to the goods they’ll transport.
Treatment Methods for Pallet Wood
Treatment methods ensure pallets meet safety standards and perform reliably across different environments. Heat treatment (HT) serves as the industry standard for killing pests and preventing insect infestations, particularly crucial for pallets used in international shipping. Kiln drying reduces the wood’s moisture content, effectively preventing fungi and mold growth that could compromise structural integrity. Chemical treatments, though less common in modern manufacturing, might still be applied to certain pallets requiring enhanced preservation properties. These treatment processes are typically marked on the pallets with exact stamps indicating the method used.
International Pallet Wood Standards and Markings
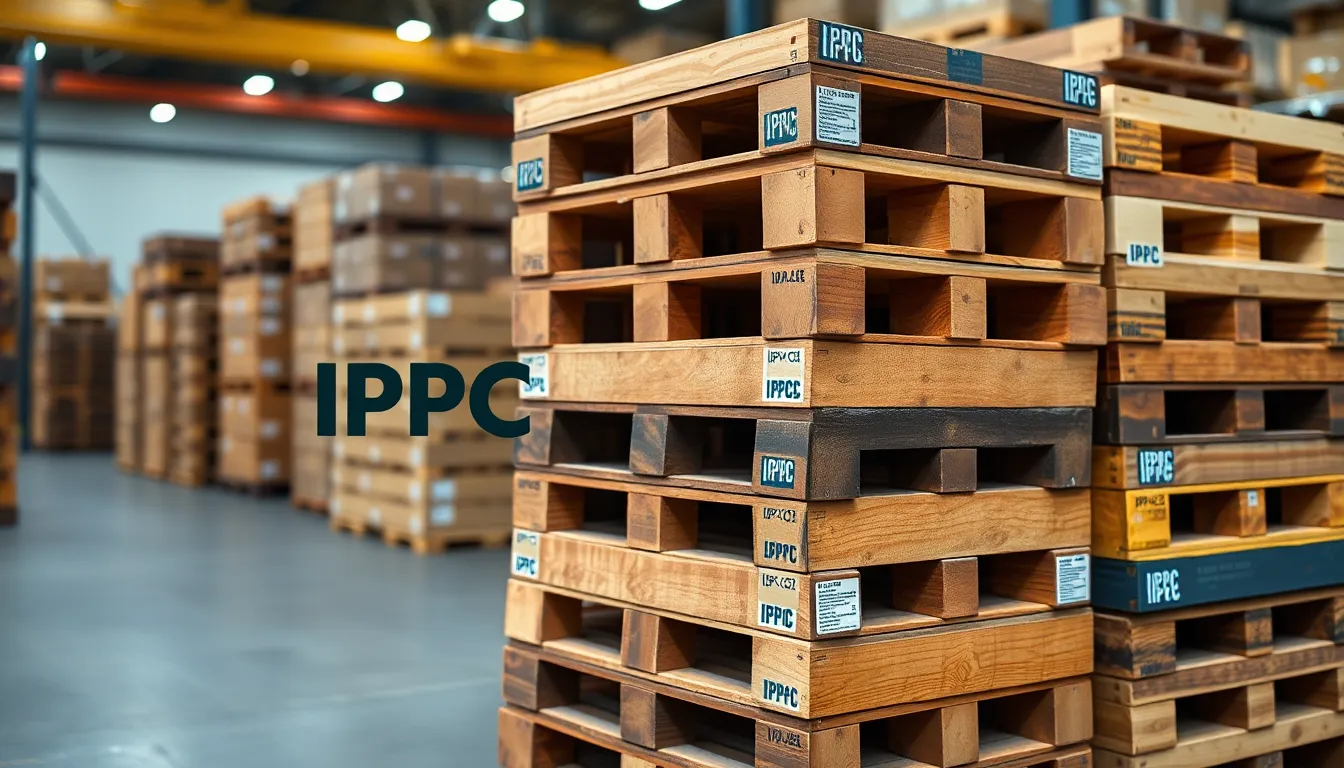
International wooden pallets follow strict guidelines to ensure safety in global shipping and prevent the spread of invasive species. These standards involve exact treatment requirements and markings that indicate compliance with international regulations.
ISPM-15 Regulations and Heat Treatment
ISPM-15 (International Standards for Phytosanitary Measures No. 15) establishes crucial requirements for wood packaging materials used in international trade. The regulations mandate that wooden pallets undergo either heat treatment or methyl bromide fumigation to eliminate pests and prevent their spread across borders. Heat-treated pallets reach a core temperature of 56°C (132.8°F) for a minimum of 30 minutes, effectively killing insects and larvae without using chemicals. This process creates a safer option for transporting goods, particularly for industries with strict contamination controls. Wood composite pallets, made from compressed wood fiber, automatically meet ISPM-15 requirements because their manufacturing process already involves high temperatures that eliminate pests.
Understanding Pallet Stamps and Codes
Pallet stamps serve as visual verification of regulatory compliance and treatment status. Each internationally approved pallet displays several important markings:
- IPPC Logo: The International Plant Protection Convention symbol confirms the pallet meets global phytosanitary standards
- Country Code: Two-letter designation indicating country of origin (e.g., US for United States)
- Producer Code: Unique identifier for the manufacturer responsible for the pallet
- Treatment Indicators: “HT” signifies heat treatment, while “KD” indicates kiln-dried wood
- DB: Confirms the wood has been debarked, reducing potential pest habitats
Unmarked pallets typically circulate only in domestic markets and don’t comply with international shipping requirements. For cross-border shipping, pallets must display the appropriate IPPC logo and treatment stamps. Over 90% of international shipping pallets use wood combined with metal fasteners, making these stamps essential for global commerce and regulatory compliance.
Quality Differences in Pallet Wood
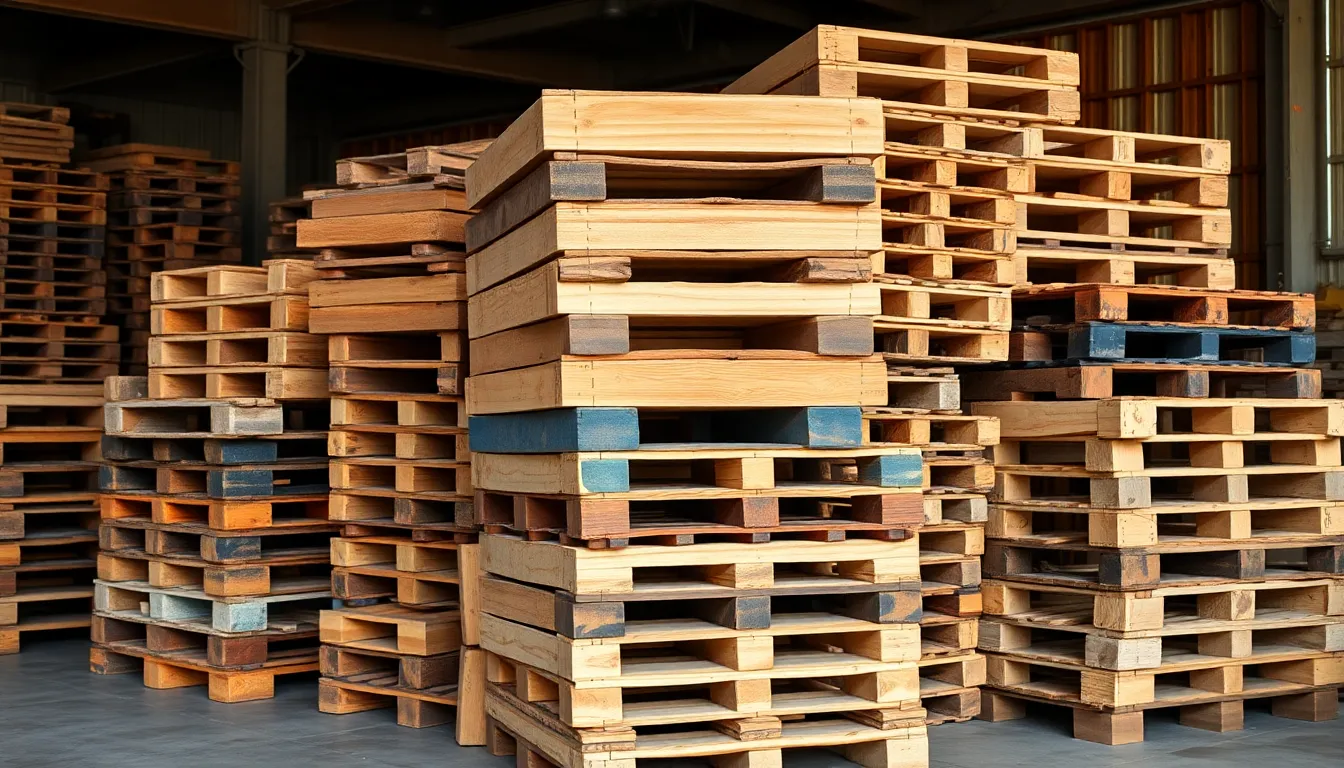
Pallet wood quality varies significantly based on several factors including the type of wood, treatment methods, and whether it’s new or recycled. Understanding these differences helps in selecting the right pallet for exact applications and determines its suitability for upcycling projects.
Hardwood vs. Softwood
Hardwoods like oak and ash offer superior durability that makes them ideal for applications requiring repeated use and heavy load capacity. These dense wood varieties withstand wear and tear significantly better than their softwood counterparts, though they come at a higher price point. Oak stands out as the most common hardwood used in pallet construction, prized for its exceptional strength and longevity.
Softwoods such as pine present a more cost-effective alternative for single-use applications where long-term durability isn’t the primary concern. Pine pallets dominate many shipping sectors due to their lighter weight, lower cost, and widespread availability. Many businesses opt for softwood pallets when shipping lighter goods or when pallets aren’t expected to make multiple trips through the supply chain.
Treatment Methods
Heat treatment represents one of the most common processes for preparing pallet wood, especially for international shipping. This method involves heating the wood to a core temperature of 56°C (132.8°F) for at least 30 minutes to eliminate pests and pathogens. Pallets that undergo this process are particularly important for sensitive industries like pharmaceuticals and food production where contamination risks must be minimized.
Softwoods like Southern Yellow Pine offer additional benefits in the treatment process as they’re easier to dry thoroughly. Their structure allows for more efficient moisture removal, which significantly reduces the risk of fungal growth and mold development during storage and transport. Properly treated pallets carry exact markings indicating their compliance with international standards like ISPM-15.
New vs. Recycled Pallet Wood
New pallets use fresh lumber that guarantees structural integrity and consistent quality throughout each component. These virgin wood pallets provide maximum load capacity and precise dimensions, making them suitable for automated handling systems and applications with strict specifications. Companies requiring exact industry certifications typically favor new pallets to ensure complete compliance with relevant standards.
Recycled pallets incorporate repaired or reassembled wood components from previously used pallets, with approximately 90% of wooden pallets involving some recycled or rebuilt timber. This approach significantly reduces waste and offers environmental benefits, though potentially with some compromise in load capacity or uniformity. Many recycled pallets undergo thorough inspection and repair processes to ensure they maintain adequate structural integrity for their intended use while providing a more sustainable option for businesses focused on reducing their environmental footprint.
Environmental Impact of Pallet Wood Production

Pallet wood production’s environmental impact spans several key areas that affect our planet’s sustainability. Deforestation remains a important concern as the timber industry expands to meet global shipping demands. Large-scale harvesting for pallet production contributes to habitat loss when not managed through sustainable forestry practices.
Recycling offers a promising solution within the pallet industry, with many manufacturers now using reclaimed wood. This circular approach helps reduce waste and decreases demand for virgin timber by extending the lifespan of existing materials. Approximately 90% of wooden pallets are either recycled or rebuilt, demonstrating the industry’s shift toward more sustainable practices.
Pest control measures present another environmental consideration in pallet production. Wood pallets require treatment to prevent insect infestation and disease transmission during international shipping. These treatments sometimes involve chemicals that may impact soil and water quality if not properly managed or contained.
Composite materials represent an innovative alternative gaining popularity in the pallet market. Made from a combination of resin and recycled wood fibers, these composite pallets offer enhanced durability while utilizing materials that would otherwise end up in landfills. Their production typically requires less virgin timber, creating a more environmentally friendly option for companies concerned about their ecological footprint.
Health and Safety Considerations for Pallet Wood
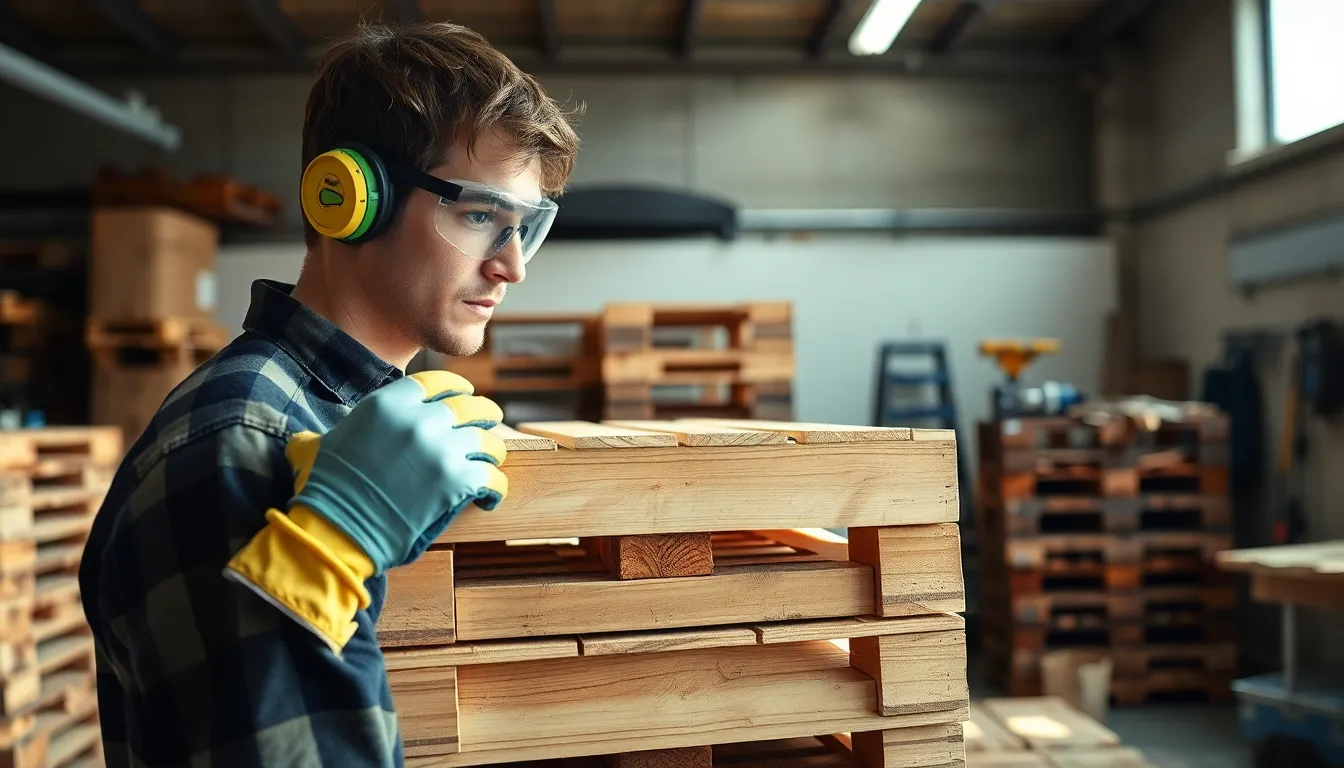
Pallet wood presents several important health and safety concerns that DIY enthusiasts should understand before starting their upcycling projects. These considerations range from chemical contamination to physical hazards that require careful attention to ensure safe handling and use.
Chemical Contamination Risks
Wooden pallets often absorb hazardous substances during their lifecycle in industrial settings. These contaminants include pesticides, chemical spills, and other toxic materials that can remain in the wood fibers. Pallets marked with “MB” indicate treatment with methyl bromide fumigation, a toxic chemical that makes them unsuitable for consumer projects, especially those involving food contact or indoor furniture.
Microbial Growth Concerns
Untreated pallet wood becomes susceptible to mold and fungi growth when exposed to moisture in storage or transportation environments. Heat-treated pallets, identifiable by the “HT” marking, significantly reduce this risk as the heat treatment process eliminates existing microorganisms. These heat-treated options comply with International Standards for Phytosanitary Measures (ISPM 15), making them a safer choice for repurposing projects.
Physical Hazards When Working with Pallets
Physical dangers constitute a major safety concern when handling used pallet wood. Protruding nails, metal staples, and splinters can cause injuries during disassembly and processing. Structural weaknesses in damaged pallets might lead to unexpected breakage during handling or after project completion. Thorough inspection before use, proper protective equipment, and careful disassembly techniques help minimize these physical risks.
Pest Infestation Prevention
Untreated wood pallets potentially harbor insects like termites, beetles, and other wood-boring pests that can spread to your home or workshop. Heat treatment effectively eliminates these pests, preventing potential infestations when bringing pallet wood indoors. Composite pallets made from resin and recycled wood fibers offer an alternative that’s exempt from ISPM 15 regulations and naturally resistant to pest infestations, making them suitable for both export purposes and DIY projects.
Repurposing Pallet Wood: What to Know First
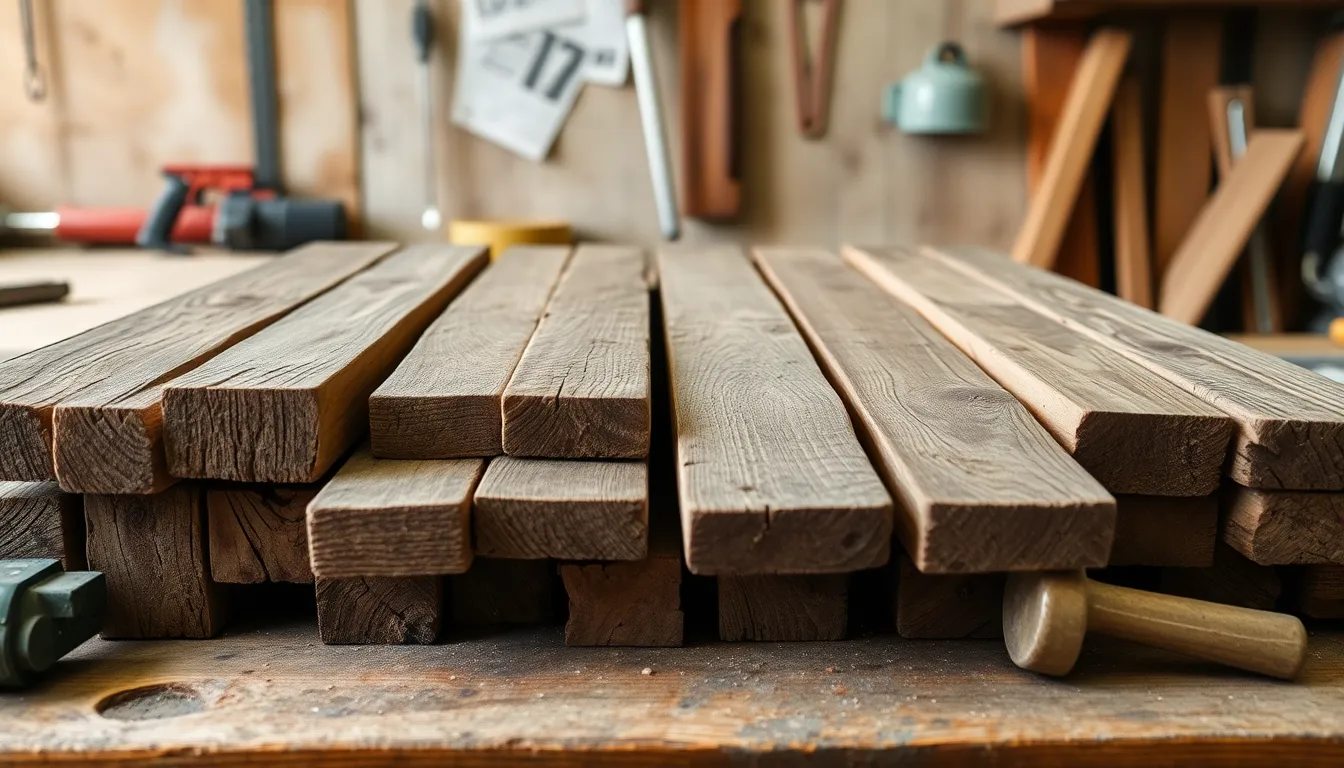
Repurposing pallet wood requires careful consideration of the wood type and treatment history before starting any project. Pine, which makes up a important portion of pallet construction, typically demands less preparation than hardwoods like oak when transforming pallets into furniture or decorative items. Over 90% of pallets are made from wood, with softwoods dominating the market due to their lightweight nature and affordability.
Before beginning your pallet wood project, always check for contaminants or chemical treatments that might be hazardous. Chemical residues from the pallet’s previous use can leach into gardens if used for planters or cause health issues when used indoors. Heat-treated pallets (marked with “HT”) are generally safer options for repurposing compared to those treated with methyl bromide.
Wood composite pallets offer another alternative for DIY enthusiasts looking for durable materials. These pallets, made from compressed wood fibers, are ISPM 15 exempt and don’t require the same level of scrutiny as traditional wooden pallets. Their consistent composition makes them easier to work with for certain projects while minimizing concerns about hidden contaminants.
Metal fasteners embedded in pallet wood present another challenge when repurposing. Thoroughly inspect each board for nails, staples, or other hardware that could damage tools or cause injury. Removing these fasteners completely before cutting or sanding helps prevent accidents and extends the life of your woodworking equipment.
Hardwood pallets, particularly those made from oak, provide excellent material for projects requiring durability and strength. These higher-quality woods can be transformed into statement furniture pieces that showcase the natural character and grain patterns unique to reclaimed pallet wood.
Prioritize pallets from domestic shipments when possible, as they’re less likely to contain harsh chemicals than those used for international transport. The authentic weathered appearance that makes pallet wood so desirable comes with potential risks that proper selection and preparation can mitigate.
Conclusion
Pallet wood offers an incredible combination of versatility accessibility and character for DIY projects. Whether you’re working with common softwoods like pine or more durable hardwoods like oak understanding the composition and treatment of your materials is essential for successful upcycling.
We’ve seen how the manufacturing process treatment methods and international standards all play crucial roles in determining pallet quality. For those looking to repurpose these materials proper selection and safety precautions can’t be overlooked.
As sustainability becomes increasingly important the pallet industry continues to evolve with recycling programs and innovative composite alternatives. By making informed choices about the pallet wood we use we can create beautiful functional pieces while minimizing environmental impact and ensuring our projects remain safe for years to come.
Frequently Asked Questions
What types of wood are commonly used in pallets?
About 80% of pallets are made from softwoods like Southern Yellow Pine, spruce, and fir due to their availability and cost-effectiveness. The remaining 20% are hardwoods such as oak, maple, and birch, which offer superior strength for heavier loads. Oak is the most common hardwood used in pallets because of its exceptional durability.
How can I tell if a pallet is safe for DIY projects?
Look for stamps indicating heat treatment (HT), which means the pallet is free from pests and generally safer for reuse. Avoid pallets marked “MB” (methyl bromide) as they contain harmful chemicals. Also inspect for stains, strong odors, or obvious chemical spills. Heat-treated, domestic-use pallets with minimal staining are your safest options for DIY projects.
What are the standard dimensions of wooden pallets?
In North America, standard pallets measure 48″ × 40″ (1219mm × 1016mm), while European pallets (Euro pallets) are typically 1200mm × 800mm. These dimensions are optimized for standard shipping containers and warehouse storage systems. The main components include deck boards (the flat surfaces), stringers (support beams), and blocks.
How are wooden pallets manufactured?
Pallet manufacturing involves selecting appropriate wood based on intended use, cutting lumber to precise measurements, and assembling with metal fasteners like nails or staples. Many pallets undergo finishing processes like sanding and treatment methods such as heat treatment or kiln drying to meet international shipping regulations and increase durability.
What do the stamps and markings on pallets mean?
Pallet stamps indicate compliance with international regulations. Key markings include the IPPC logo, country code (e.g., “US” for United States), producer code, treatment indicators (HT for heat treatment or MB for methyl bromide), and debarking confirmation. These stamps are essential for cross-border shipping and provide information about the pallet’s origin and treatment.
Are recycled pallets as good as new ones?
New pallets offer maximum load capacity and consistency but at a higher cost. Recycled pallets provide environmental benefits and cost savings but may have reduced structural integrity or inconsistent quality. For DIY projects, recycled pallets often work well, but for industrial use requiring specific load capacities, new pallets may be preferable.
What health risks should I be aware of when working with pallet wood?
Potential risks include chemical contamination from substances absorbed during use, particularly in methyl bromide-treated pallets. Untreated pallets may harbor mold, fungi, or bacteria. Physical hazards like protruding nails and splinters are common. Always wear protective gear, thoroughly clean pallets, and avoid those with unknown history or chemical markings.
How environmentally friendly is pallet wood production?
The industry has improved sustainability, with approximately 90% of wooden pallets being recycled or rebuilt. This reduces waste and decreases demand for virgin timber. However, concerns remain about deforestation and chemical treatments affecting soil and water quality. Composite pallets, which combine resin and recycled wood fibers, offer an eco-friendly alternative.
What tools do I need to disassemble a pallet for DIY projects?
Essential tools include a pry bar or nail puller, hammer, reciprocating saw, safety glasses, work gloves, and a flat work surface. A nail punch helps remove stubborn nails safely. For efficiency, consider specialized pallet busters or dismantling tools. Always prioritize safety by wearing appropriate protective equipment throughout the disassembly process.
Which type of pallet wood is best for making furniture?
Hardwood pallets (oak, maple, ash) are ideal for furniture due to their durability, strength, and attractive grain patterns. They’re better suited for weight-bearing pieces like tables and chairs. Softwood pallets (pine, spruce) work well for decorative items or non-structural elements. Always select pallets that are heat-treated (HT) and free from chemical contamination.