Wondering if your pressure treated wood needs sealing? You’re not alone. Many homeowners invest in pressure treated lumber for outdoor projects but remain unsure about the next steps to maximize its lifespan and appearance.
We’ve helped thousands of DIY enthusiasts and professionals navigate this common question. While pressure treated wood is designed to resist rot and insect damage, sealing it can provide additional benefits you won’t want to miss. In this comprehensive guide, we’ll explore whether sealing is necessary, the advantages it offers, and how to properly protect your investment for years to come.
What Is Pressure Treated Wood?
Pressure treated wood is lumber that’s been infused with chemical preservatives to protect it from rot, fungal decay, and insect attacks. These preservatives significantly extend the wood’s lifespan compared to untreated lumber, making it an excellent choice for outdoor applications where moisture exposure is common.
How Pressure Treatment Works
The pressure treatment process involves placing dried lumber into a large cylindrical chamber called a retort. Powerful vacuum and hydraulic systems force preservative chemicals deep into the wood’s cellular structure under high pressure. This method ensures the preservatives penetrate completely through the wood rather than just coating the surface. Common preservatives include alkaline copper quaternary (ACQ), copper azole (CA), and micronized copper quaternary (MCQ), which have replaced the older chromated copper arsenate (CCA) treatments due to environmental and health concerns. The distinct greenish or brownish tint often visible on pressure treated lumber comes from these copper-based preservatives.
Common Uses for Pressure Treated Wood
Pressure treated lumber dominates outdoor construction projects due to its exceptional durability in challenging environments. Decks, fences, and pergolas represent the most popular applications for this material, as these structures face constant exposure to moisture and ground contact. Industry timbers, garden beds, and outdoor furniture also benefit from pressure treatment, especially when soil contact is unavoidable. Marine applications like docks and boardwalks rely heavily on pressure treated wood specifically rated for saltwater environments. Playground equipment and support posts for buildings often use pressure treated lumber since these structural components must withstand both weather exposure and weight-bearing responsibilities. When choosing pressure treated wood, it’s essential to select the appropriate retention level based on your project’s exact exposure conditions.
Does Pressure Treated Wood Need to Be Sealed?
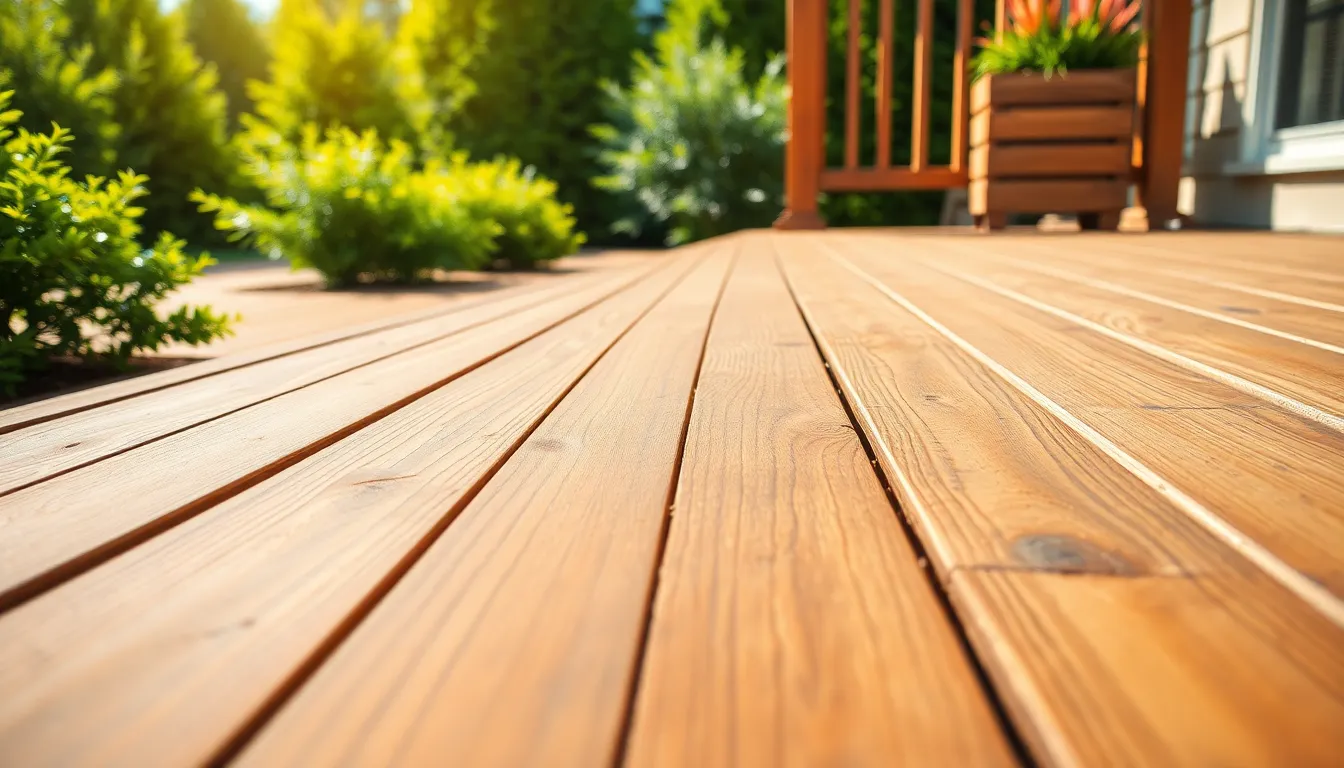
Pressure treated wood benefits from sealing even though its inherent resistance to biological threats. The chemical treatment provides important protection against rot, decay, and insects, but sealing offers additional benefits that extend the wood’s life and appearance.
Initial Protection From Treatment
Pressure-treated lumber comes pre-protected with copper-based preservatives that penetrate deep into the wood fibers. This chemical treatment creates a robust defense system against rot, decay, and insect damage, giving the wood structural integrity that untreated varieties lack. The preservation process focuses primarily on biological threats rather than physical elements. Even though this impressive initial protection, the treatment doesn’t safeguard against moisture penetration, UV damage, or everyday wear and tear that outdoor wood regularly experiences.
Factors That Impact Sealing Decisions
Moisture exposure plays a critical role in determining whether to seal pressure-treated wood. Untreated moisture absorption causes the wood to swell, shrink, and eventually warp or crack as it moves through wet-dry cycles. Applying a quality sealant creates an effective barrier that prevents water from infiltrating the wood’s surface.
UV protection becomes essential for maintaining the wood’s appearance over time. Sunlight gradually fades pressure-treated lumber, turning it a weathered gray color. Sealing dramatically slows this color degradation process, helping maintain the wood’s original appearance.
Drying time must be considered before applying any sealant. While older guidelines recommended waiting up to 6 months before sealing new pressure-treated wood, modern treatments with micronized copper may require as little as 30 days of drying time. Testing wood readiness by sprinkling water on the surface offers a reliable indicator – if water beads up, the wood isn’t ready; if it absorbs, you’re clear to seal.
Location significantly impacts sealing requirements. Indoor applications might not demand sealing unless moisture resistance or aesthetic enhancement is prioritized. Outdoor installations, but, strongly benefit from proper sealing to combat the elements and extend the wood’s useful life.
Regular maintenance ensures ongoing protection. Sealants typically need reapplication every 1-3 years depending on weather exposure and traffic. Using products specifically designed for pressure-treated wood ensures compatibility with the chemical preservatives already in the lumber.
Benefits of Sealing Pressure Treated Wood
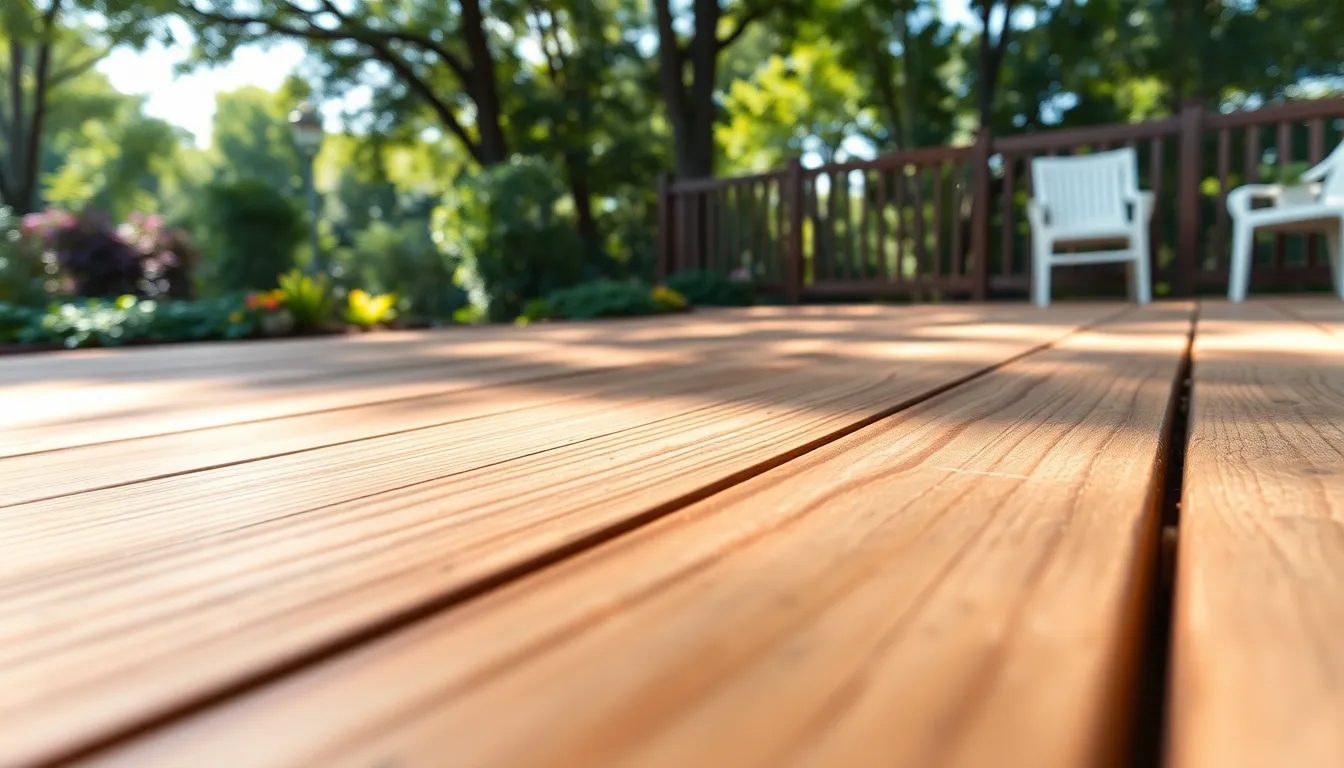
Sealing pressure treated wood provides crucial protection beyond its initial chemical treatment. The preservatives in pressure treated lumber defend against rot and insects, but sealing addresses other vulnerabilities that can significantly impact its performance and longevity.
Extended Lifespan
Pressure treated wood’s lifespan increases dramatically when properly sealed. Unprotected wood experiences moisture absorption and drying cycles that cause expansion and contraction, leading to warping, cracking, and structural weakening over time. Sealing creates a moisture barrier that prevents this damaging cycle, helping properly maintained pressure treated decks last 15-20 years. Regular reapplication of sealant every 1-3 years maintains this protective barrier and ensures the wood remains structurally sound throughout its service life.
Improved Appearance
Sealing enhances and preserves the aesthetic qualities of pressure treated wood. Unsealed wood quickly develops a weathered gray appearance from UV exposure and can become discolored from mold and mildew growth. A quality sealant with UV inhibitors prevents this fading and maintains the wood’s natural color and texture. Many sealants also contain water repellents that prevent the dark spotting and staining that occurs when moisture penetrates the wood surface. This protection keeps outdoor structures like decks and fences looking fresh and well-maintained for years rather than months.
When to Seal Pressure Treated Wood
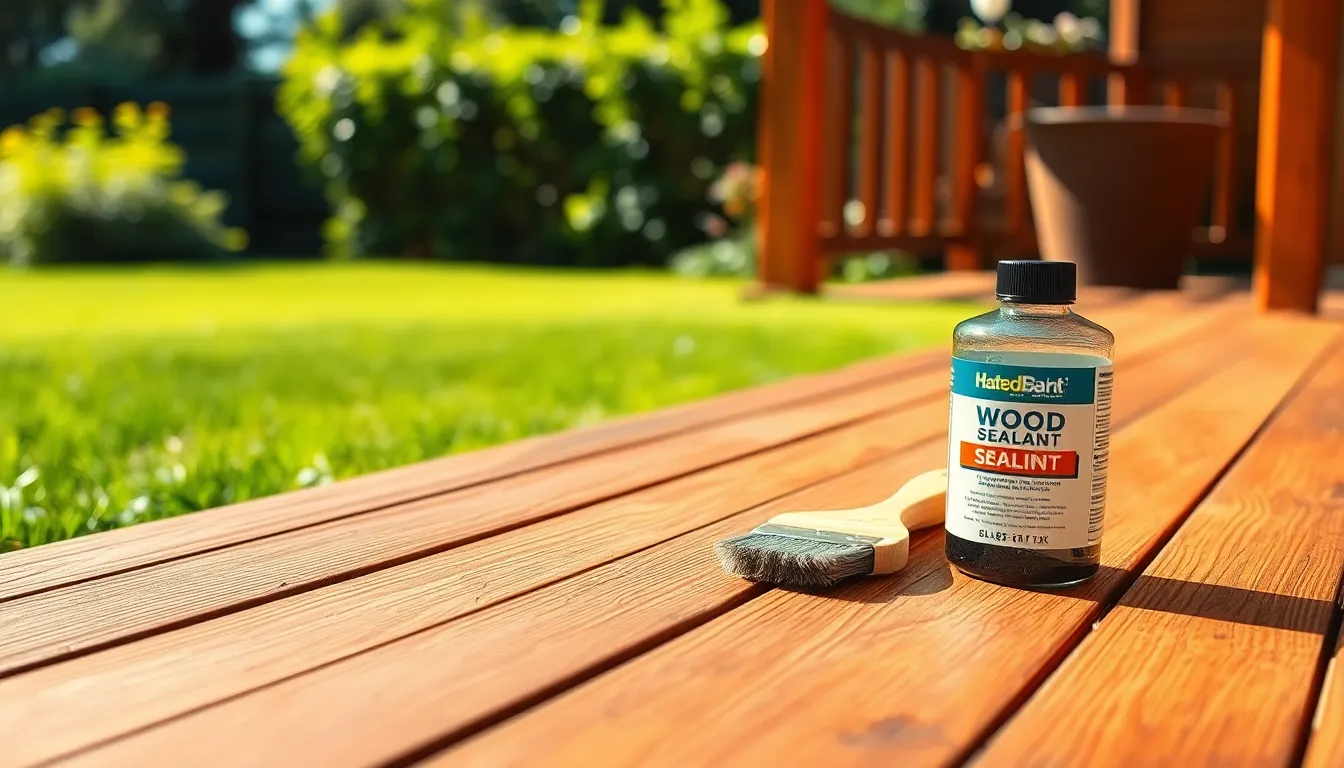
Timing is everything when sealing pressure-treated wood for maximum protection and longevity. Proper sealing at the right moment ensures your outdoor structures remain resistant to moisture damage and UV deterioration beyond the basic protection offered by the chemical treatment process.
Timing After Installation
Patience proves essential when planning to seal newly installed pressure-treated lumber. The wood needs to dry completely before applying any sealant, a process that typically takes several weeks to months depending on your local climate and sun exposure. Manufacturers like YellaWood specifically recommend sealing within six weeks of completing your project if using a clear water repellent. This timeframe allows the wood to properly acclimate while still being protected before excessive environmental exposure occurs. Climate factors significantly impact drying time—hot, dry regions may prepare wood for sealing faster than humid or cool areas.
Signs Your Treated Wood Needs Sealing
Recognizing when pressure-treated wood requires sealing helps prevent premature deterioration. Perform the “bead test” by sprinkling water on the surface—if it no longer forms beads but instead absorbs into the wood, it’s time to apply a new coat of sealant. Visible surface cracks or warping indicate the wood has been exposed to prolonged moisture cycles without adequate protection. Color changes provide another clear indicator, as UV damage causes graying or discoloration of previously treated lumber. Annual inspection reveals these signs early, allowing you to maintain your wood with sealants containing UV stabilizers before important damage occurs. Oil-based or water-repellent sealants designed specifically for treated lumber deliver optimal results when applied to clean, dry surfaces.
Best Sealants for Pressure Treated Wood
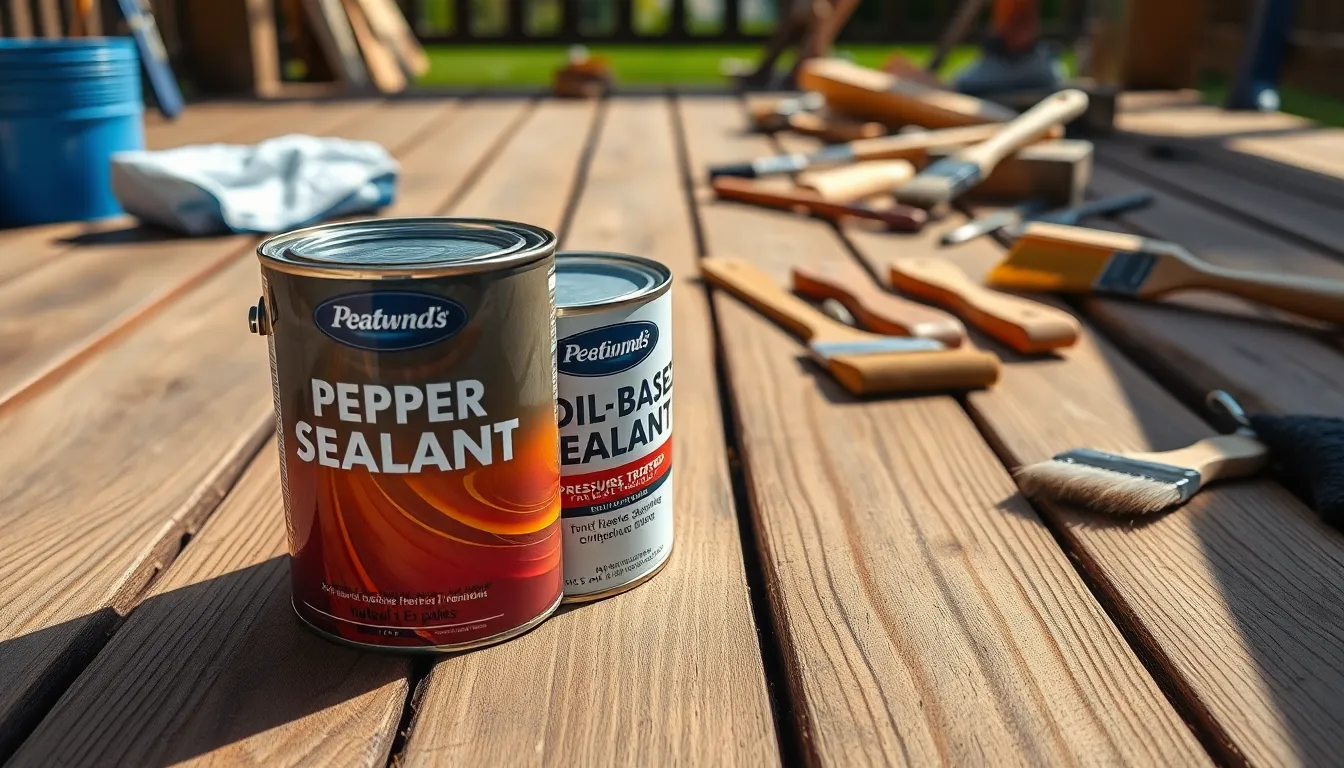
Selecting the right sealant for pressure treated wood significantly impacts its longevity and appearance. The market offers various formulations, each with distinct properties suited for different applications and environmental conditions.
Water-Based Sealers
Water-based sealers provide excellent protection for pressure treated wood while offering several practical advantages. These sealers penetrate effectively into the wood grain and dry quickly, making them perfect for areas frequently exposed to moisture. Many homeowners prefer water-based options due to their reduced volatile organic compound (VOC) emissions, creating a safer application environment. These formulations typically include mildew-resistant properties, essential for maintaining wood’s appearance in humid climates. Application requires fewer tools and cleanup involves simple soap and water, eliminating the need for harsh chemicals or solvents.
Oil-Based Options
Oil-based sealants deliver superior penetration and durability, particularly beneficial for high-traffic outdoor structures like decks and stairs. These formulations enhance pressure treated wood’s natural grain patterns and color depth, resulting in a richer aesthetic appeal than many water-based alternatives. Professional contractors often recommend oil-based products for their extended protection periods, though they require longer drying times between coats. The deep penetration creates a robust moisture barrier that helps prevent warping and splitting in extreme weather conditions. Applications typically last longer between maintenance cycles, reducing the frequency of reapplication compared to water-based counterparts.
How to Properly Seal Pressure Treated Wood
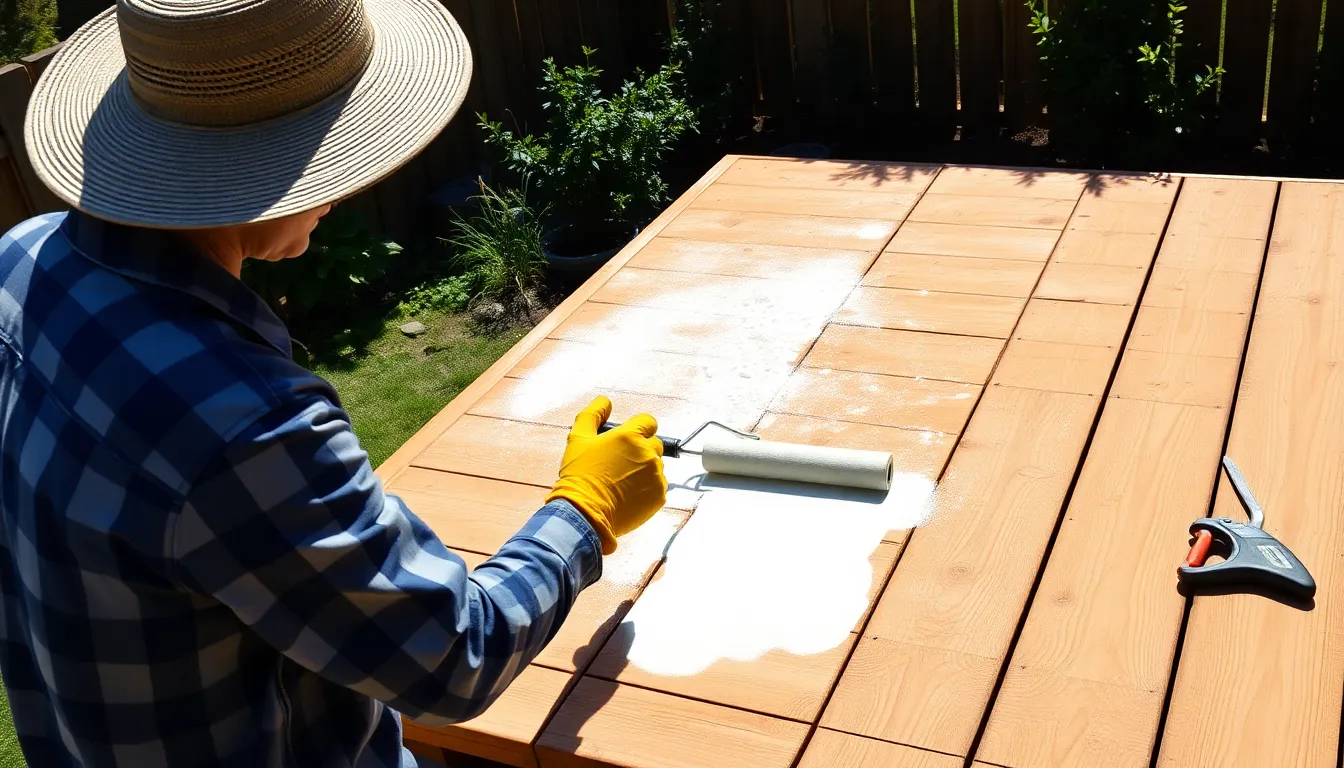
Sealing pressure treated wood requires proper technique and timing to maximize protection. The process involves waiting for the wood to dry completely, testing its readiness, and applying an appropriate water-repellent sealer.
Step-by-Step Application Process
Preparing the surface starts with thoroughly cleaning the pressure treated wood to ensure proper sealer adhesion. Sweep away all debris and dirt, then wash the surface with a deck cleaner to remove any mildew, algae, or contaminants that might interfere with the sealing process. Allow the wood to dry completely after cleaning before moving forward with sealer application.
Testing the wood’s readiness comes next by performing the simple “bead test” – sprinkle water droplets on the surface and observe their behavior. When water forms beads that sit on top rather than absorbing quickly, your pressure treated wood is ready for sealing. This indicates the wood has dried sufficiently and will accept the sealer properly.
Applying the sealer requires even distribution using a brush, roller, or sprayer depending on your project size. Work in small sections, applying the sealer along the grain of the wood for maximum penetration and coverage. Pay special attention to end grains and joints where moisture tends to penetrate more easily. Avoid applying sealer in direct sunlight or when rain is expected within 24-48 hours.
Drying time varies based on the product specifications, weather conditions, and humidity levels. Most sealers require at least 24-48 hours to dry completely before the surface can handle normal foot traffic or furniture placement. Following manufacturer guidelines about drying times ensures optimal protection and performance from your sealer.
Maintenance Schedule
Regular inspections form the foundation of an effective maintenance schedule for sealed pressure treated wood. Examine your wood structures every 3-6 months for signs of wear, including water absorption, cracking, splintering, or color fading. These visual indicators help determine when resealing becomes necessary before important damage occurs.
Annual reapplication provides optimal protection in most climate conditions. Areas with harsh weather, heavy rainfall, or intense sun exposure may require more frequent sealing—potentially every 6-9 months. Northern climates with freezing temperatures and snow might need special attention before winter sets in to prevent moisture damage during freeze-thaw cycles.
Cleaning between applications improves sealer performance and extends the wood’s lifespan. Before reapplying sealer, wash the surface with an appropriate wood cleaner and allow it to dry completely. Remove any peeling or flaking areas from previous sealer applications to ensure the new coat adheres properly and provides consistent protection.
Documentation of maintenance activities helps track the performance of different products and establishes an effective care routine. Keep records of when you last sealed the wood, which products you used, and any issues you encountered or resolved. This information proves invaluable for determining the most effective maintenance schedule for your exact pressure treated wood structures.
Conclusion
Pressure treated wood doesn’t absolutely require sealing but doing so delivers important benefits that justify the effort. By applying a quality sealant you’ll extend your wood’s lifespan protect against moisture damage and maintain its appearance through years of outdoor exposure.
Remember that timing matters – allow new pressure treated lumber to dry completely before sealing and commit to regular maintenance checks every 3-6 months. With proper care your outdoor structures can last 15-20 years while retaining their strength and beauty.
The small investment in time and materials to seal and maintain your pressure treated wood projects will pay dividends through reduced replacement costs and continued enjoyment of your outdoor living spaces for years to come.
Frequently Asked Questions
Is it necessary to seal pressure treated wood?
While pressure treated wood is already resistant to rot and insects, sealing provides additional protection against moisture penetration and UV damage. Sealing helps prevent warping, cracking, and color degradation, significantly extending the wood’s lifespan. For optimal protection and appearance, sealing is recommended despite the inherent durability of pressure treated lumber.
How long should I wait before sealing new pressure treated wood?
Allow newly installed pressure treated lumber to dry completely before sealing, typically 30-60 days depending on climate conditions. Modern treatments may require as little as 30 days, while older treatments might need longer. Manufacturers generally recommend sealing within six weeks of installation if using a clear water repellent. Test wood readiness using the “bead test” before applying sealant.
How often should I reseal my pressure treated wood?
Pressure treated wood should be resealed every 1-3 years, depending on exposure conditions. Areas with high sun, rain, or snow exposure may need more frequent reapplication. Regular inspections every 3-6 months help determine when resealing is necessary. Document your maintenance schedule to establish an effective care routine for your specific environmental conditions.
What are the signs that my pressure treated wood needs sealing?
Look for water absorption (failed “bead test”), visible cracks or warping, color fading from UV exposure, and gray weathering. Other indicators include rough texture, splintering, or visible mold and mildew growth. Regular inspections of your outdoor structures will help identify these warning signs early, allowing you to maintain the wood’s protection before significant damage occurs.
What type of sealer is best for pressure treated wood?
Choose between oil-based sealers (offering deeper penetration and longer protection) or water-based sealers (environmentally friendly with easier cleanup). For optimal results, select products specifically designed for treated lumber that contain both UV inhibitors and water repellents. Consider your local climate conditions and the wood’s exposure level when making your selection.
Can I stain pressure treated wood instead of sealing it?
Yes, you can use a combination stain-and-sealer product that both colors the wood and provides protection. These products serve dual purposes by enhancing the wood’s appearance while creating a protective barrier against moisture and UV damage. Ensure the product is specifically formulated for exterior use on pressure treated lumber for best results.
How do I properly apply sealer to pressure treated wood?
Clean the wood thoroughly using a deck cleaner to remove dirt and debris. Allow the wood to dry completely. Apply the sealer using a brush, roller, or sprayer following the manufacturer’s instructions. Work in small sections, maintaining a wet edge to prevent lap marks. Apply thin, even coats rather than one thick coat for better absorption and protection.
Does sealed pressure treated wood last longer?
Yes, sealed pressure treated wood lasts significantly longer than unsealed wood. While untreated lumber might last 2-5 years outdoors, properly maintained pressure treated wood can last 15-20 years or more. The sealer prevents moisture damage, UV deterioration, and premature aging, maximizing your investment in outdoor structures.